Trends and Emerging Technologies in Sheet Metal Fabrication
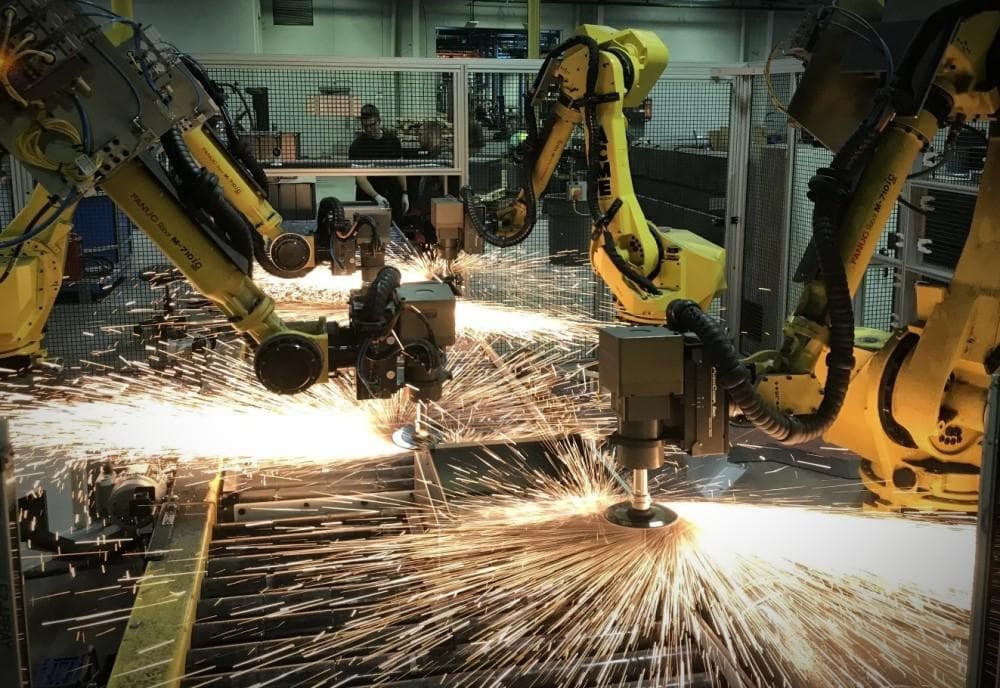
The metal fabrication industry has seen many technological advancements in the recent years, automation, digitization, and the other technologies have not only helped optimize and speed up industrial metal fabrication processes, but also allowed for more customizations of products to fit the specific needs of customers. These growing trends have contributed to the exponential growth of the industry.[i] By the end of 2031, the metal fabrication industry is estimated to reach a market value of $473.7 billion, a significant surge in value from $362.4 billion in 2020. The main reason behind the growth is the increasing demand of metal fabrication within various industries like manufacturing, automotive, defense and aerospace. Automation and other important technologies are key drivers of growth in the industry that continue to make the metal fabrication more efficient and profitable. Examples of these technological trends include Automation, Robotics, Cybersecurity, 3D printing, Reshoring of labor, Adopting lean manufacturing methodologies, and Digitization.
Automation
Automation has significantly impacted the industry making the processes more efficient and productive by integrating automated machinery with computer numerical control machinery that work to eliminate any inaccuracies and mistakes in repetitive processes being carried out. The entire purpose of automation is to minimize the need for human labor in the manufacturing process, and, also, in time to optimize the process by continuously learning and improving the ways in which the machines carry out their tasks. For instance, cutting with a portable torch is never an exact procedure, even when done by an experienced expert. When producing metal, automation eliminates human error, resulting in fewer cutting errors and material waste. Operating expenses drop when there is less waste.[ii]
Robotics
A wide range of robots can be designed and used in the metal fabrication industry, some may work as standalone robots that carry out specific menial tasks like plasma cutting, whereas some others may be a key participant in the automated manufacturing processes. The most common robots that you might encounter are Articulated robots, Cartesian robots, Delta robots, and SCARA (selective compliance assembly robot arms) robots.[iii] Collaborative fabrication robotics are put in use in the industry to perform tasks that can be life-threatening for humans and carry out repetitive tasks with extreme precision. Similarly, robots are able to produce better quality output, and reduce overhead costs for companies. Although, robotics reduces the need for human labor, thus significantly reducing the availability of jobs, it also generates new jobs that require humans to operate the machinery.
Cybersecurity
Businesses of all sizes are targeted in the metal fabrication industry. Cyberattacks cost businesses $200,000 on average, and four in 10 companies have experienced multiple incidents. Research indicates ransomware attacks against companies had tripled in 2020 in over one year alone, 43 percent of the cyberattacks were made at small companies. As a reason, businesses have become more vigilant to attacks of such kind and have begun implementing measures against cyber threats to reduce the chances of data breach. [iv]
3D Printing
3D Printing, also known as additive manufacturing, provides more opportunities for customization of products, allowing customers to design products of any type, and, at the same time, reducing the overall waste generated in the process. Through additive manufacturing one can produce anything that can be designed on a computer, even human organs are produced using the same method. This is 3D printing taken to its maximum, enabling optimization of design, materials, production, and distribution, according to Siemens.
Reshoring Labor
Outsourcing manufacturing has been an integral part of many industries over the decades. However, in the case of metal fabrication, the opposite is true. Rising costs production costs in foreign countries have forces US bases metal fabrication companies to rethink their business models and considering bringing operation back home. Thus, in a way, this only allows the companies to produce more innovative and customized products but also increase job oppurtunies for American citizens.
Adopting lean manufacturing methodologies
As the name suggests, lean manufacturing is the process of reducing production steps, in turn, reducing the amount of waste generated. The whole idea is to make the production more cost-effective. It also helps companies improve their delivery, reliability, and quality.[v]
Digitization
A significant number of metal fabrication industries have introduced digital technologies like electronic tools and devices that generate, process and store relevant information, with which companies can increase their productivity by merging them with the human workforce. Digitization helps gather, measure, and analyze information that can identify gaps and deficits in efficiency and productivity.
Lastly, these trends and technological advancements are the key drivers of growth in the industry. Automated machinery, collaborative robots, and so on, enable the companies to produce higher quality products, while at the same time reducing costs by implementing lean manufacturing processes that reduce the production of waste. Business implementing these processes and technology have been successful in gaining an edge over their competitors as they are able to anticipate changes better.---