🦾 Digital Twins in Manufacturing
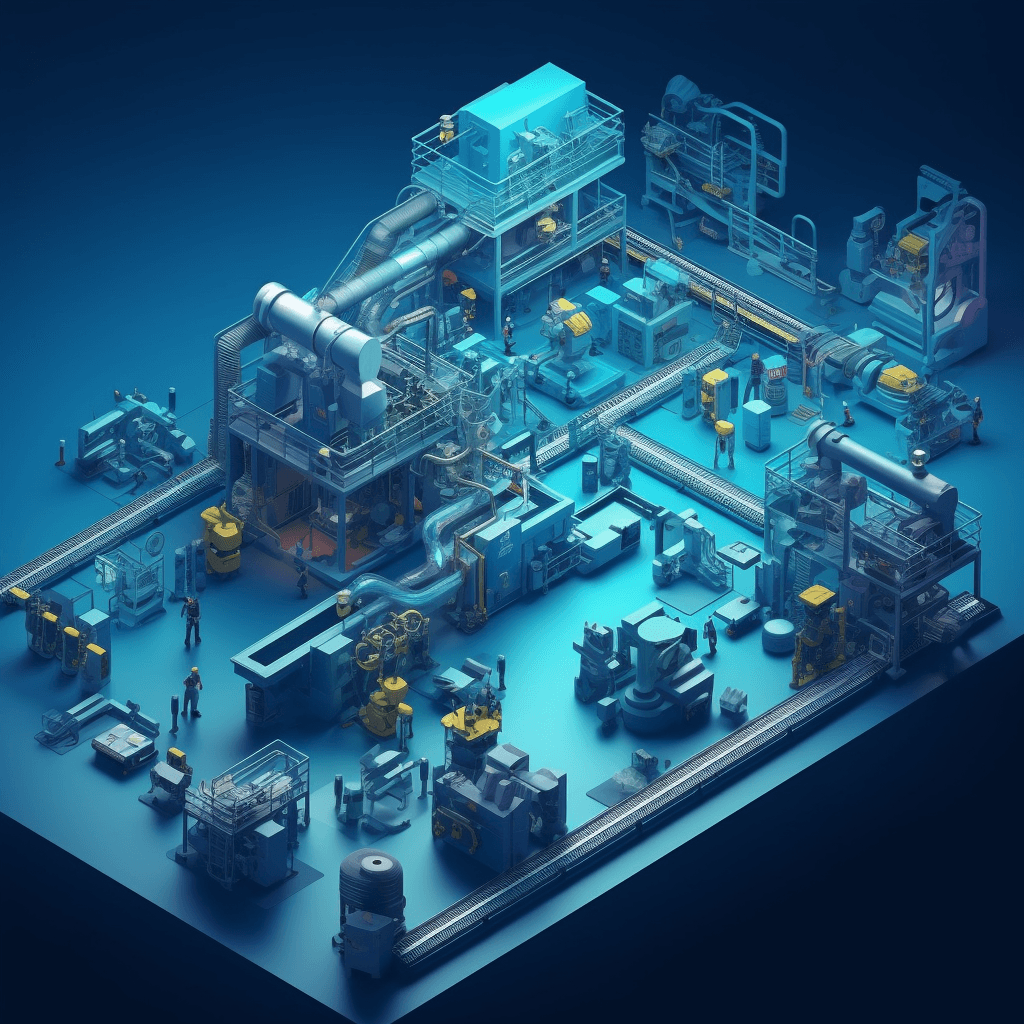
Welcome to the future of industry where digitalization is king. In recent years there’s clearly been a shift towards digital design and production processes, in the name of enhancing productivity, quality, and performance. ‘Industry 4.0’ as they’re calling it. The challenge being: how do we bridge the gap between the physical and digital worlds? Is there a solution that can accelerate the business process by reducing cost and increasing production. Enter Digital Twins (DTs).
What is Digital twin technology? A digital twin is a model that collects real time input from a physical system and accurately represents it virtually. This allows you to monitor the present state of their system as well as simulate varieties of potential scenarios.
DT isn’t brand new tech. In fact the first time the concept was applied in manufacturing was 2002 by Michael Grieves. In 2010, NASA’s John Vickers formally proposed DT and coined the term “Digital Twin”.
So, why are we stressing on now and the future? According to tech trend gurus at Gartner, DT technology will hit its stride in the next 5 to 8 years. With the rise of 5G and industrial IoT platforms, we're on the brink of a global DT boom. As we step into the era of Industry 4.0, DTs will play a pivotal role in the leap from Industry 3.0. Since 2014, Companies like Siemens, Dassault, PTC and ESI have been using the term “Digital Twins” in their marketing campaigns. It's now not only used in manufacturing, but has been applied to a variety of fields including (but not limited to) urban planning, medicine, aerospace engineering and retail.
Automotive manufacturers have taken the technology to revolutionize the way cars are made. Ford develops seven digital twins for each model of vehicle it produces. Each twin covers a different aspect of production from design to build and operation. They also use digital models for the manufacturing process, production facilities and customer experience. In their production facilities, the digital twin accurately detects energy losses and pinpoints areas where energy can be conserved and overall production line performance is improved.
Traditional project design processes typically start with requirements, then implementation, testing and then iterating through the process. With different departments being required to interact, information is bound to be the victim of some (albeit potentially minor) human error. This results in inefficient design. DT can manage all kinds of information in a unified way, and different departments can access data from DT at any time, allowing departments to work parallel to each other.
The manufacturing industry has already implemented DT in actual production. In the manufacturing cycle, DT can optimize every step.
Product designers simulate and analyze product reliability. This leads to design improvement which improves product usability. Manufacturing becomes safer and more reliable. Labor costs are reduced when intelligent equipment can be used to achieve equipment operation automation and unmanned operation. The production process can now be monitored at every step to ensure normal operation as well as to ensure product quality. Quality Inspection consumes a lot of human material and resources. DT simplifies this. AI discovers products that don’t meet the quality standard and is able to analyse the cause of the problem much faster than a human worker can. This can also inform the design of future generations. Users are afforded with a holistic understanding of the product which makes it more attractive since it is much easier to use then. Another example is Strata - a manufacturer of precision agricultural machinery - who has put digital twin technology to use, and has seen increased efficiency. To analyze data that allows farmers to make accurate decisions and react quicker to elemental and environmental conditions like storms or crop disease. The company has developed the sort of precision insights that let farmers react in moments to real world data by utilizing sensors in machinery that feed into a digital twin.
Digital twins not only reduce wasted time in product development, they save time and money in making manufacturing systems run in the most efficient and reliable way possible. At the moment only a handful of companies have adopted this kind of technology, however they seem to be potentially invaluable to innumerable sectors. With DT software becoming more sophisticated and reliable, it seems like it will be only a matter of time till it is commonplace in most industries.